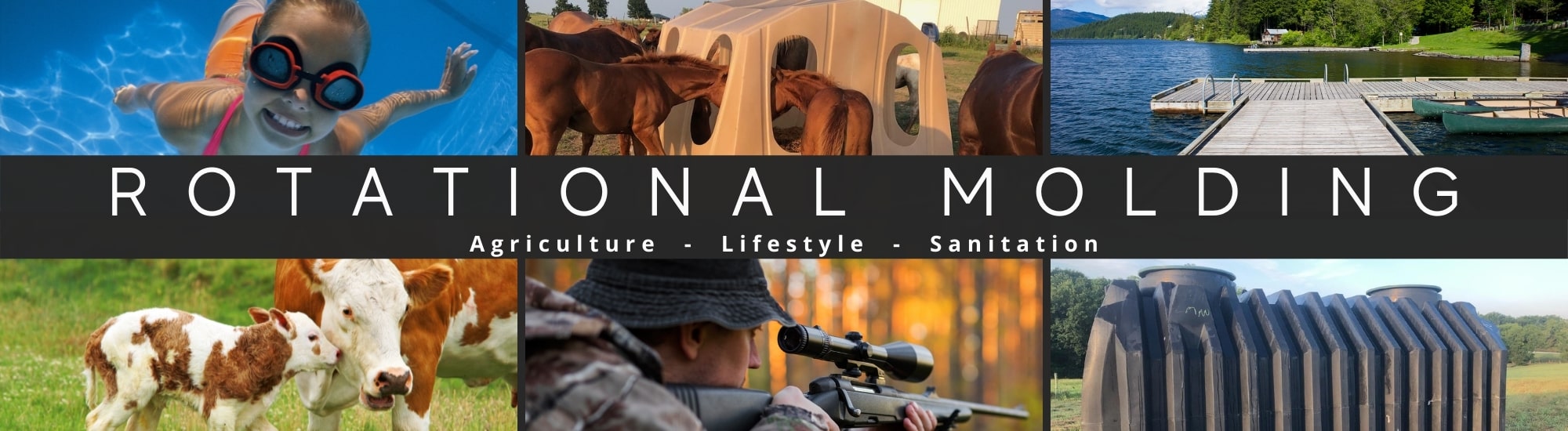
Home » Rotational Molding
Rotational Molding Process
Rotational molding is a relatively simple process of placing a powdered base plastic (typically Polyethylene) inside of a mold and then heating until it melts into a viscous liquid. The fluid is then rotated around a central axis until it has fully covered the entire internal surface of the mold and then allowed to cool. The end product is hollow, yet lightweight and extremely durable for both indoor and outdoor uses.
There are numerous advantages for rotational molding over other processes such as injection molding.
- Design Variation – the design possibilities for rotational molded products are virtually endless. If you can think it, we can probably make it.
- Lower Production Costs – the per piece production cost is typically less than other types of plastics production with greater design flexibility and end-product durability.
- Cheaper Molds – mold production is typically cheaper allowing for lower production run costs as well as the ability to change and update designs more frequently.
- Hollow Pieces – most all products produced via rotational molding are hollow. This allows for allows for major savings on weight while maintaining very high tensile strength and design integrity. These hollow cavities can be injected with variety materials to provide insulation or additional strength.
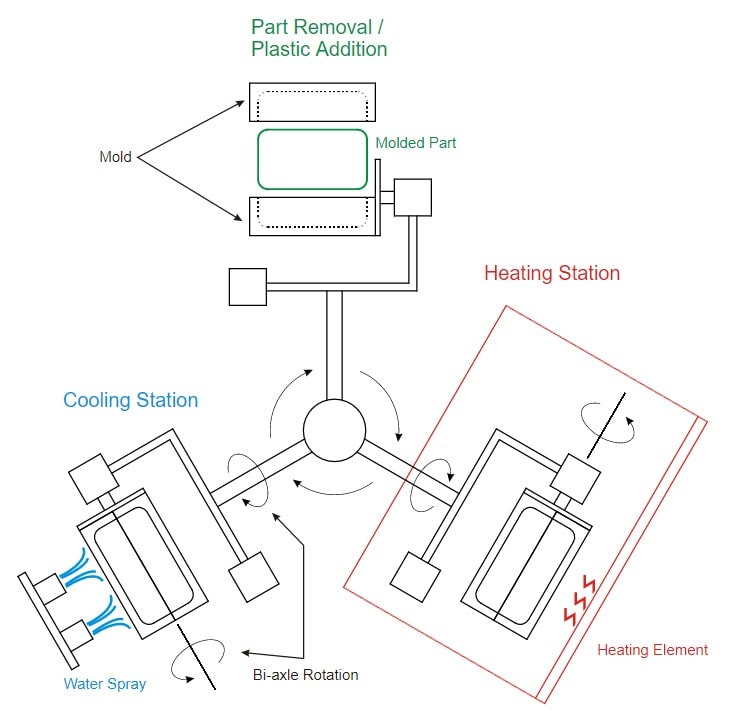
The Coon Difference
Learn Why Coon Manufacturing, Inc is the Top Rotational Molding Company in Our Region and Why You can Trust Us to Complete Your Custom Project.
It all comes down to experience and dedication to quality and we have both. Here are a few other reasons why you should choose Coon Manufacturing for your next project:
- No Production Minimums – We understand that sometimes companies with limited budgets just want to try out a particular product or concept before committing to large production runs. We’ve build a solid reputation in the industry of taking on just about every project regardless of size or scope. Many of our largest customers started off small and that’s why we truly want to help everyone bring their designs to full production.
- Large Format – The machines in our facility have a production capacity of 8’ X 14’. While other manufactures boast about a 20’ capacity, they often don’t mention that the other dimension is only 4’ which is far too restrictive when it comes to producing large industrial containers such as septic tanks and large trash bins that need to be one piece and not fastened together from multiple parts. These production sizes exponentially open up the possibilities for all types of industrial and agricultural products.
- Exceptional Customer Service – Every project and every product is completely different and we recognize that. We will walk you through every step of the process from concept to design to production. You’ll have direct access to a dedicated project manager who will make 100% certain that you fully understand all of the aspects of your project and that everything stays on schedule.
- Experience – We’ve been doing this a long time and there are many reasons why our customers keep coming back again and again.
Get a Quote
Give us a call or shoot us an email about your product or need and let our team put together a detailed price quote and production specifications. We are looking forward to hearing from you.